Is Machine Vision Surpassing the Human Eye for Accuracy?
Artificial intelligence in machine vision provides a level of precision that is equal to, and in some cases, even better than human inspection.
The idea behind machine vision, or artificial vision, is to enable industrial automation systems – via image processing – to perceive the outside world in a way that is completely analogous to the sight of a human being. Aimed at evaluating the salient features of the product under analysis, machine vision exploits the acquisition of images through cameras and their subsequent processing using image processing algorithms.
Machine Vision: Many Advantages Covering Many Needs
The adoption of machine vision overcomes the limits of traditional sensors. Sensors based on contact technologies are typically constrained by proximity, whereas the size of the inspected field typically limits sensors based on laser technologies. Implementing machine vision solutions can be the best-performing choice and the most cost-effective option due to the relatively low cost of the sensor hardware. This is especially true for applications with configurable vision sensors that do not require the use of an external PC.
Machine vision, or artificial vision, enables industrial automation systems – via image processing – to perceive the outside world in a way that is completely analogous to the sight of a human being.
Machine vision solutions offer higher levels of reliability and efficiency than traditional solutions. Thanks to their intrinsic flexibility, they can also reduce time-to-market. Only software reprogramming or reparameterization is necessary to change the task or to commission a new plant.
The industrial application fields affected by artificial vision are attributed to the following operations:
- Position detection: Specific objects are detected, and their presence or coordinates (position and orientation) are made available
- Inspection: Image analysis checks the quality of the product, the completeness of the parts of an assembly, or the presence of defects
- Measure: The characteristics of an object are acquired in one or more of three dimensions (length, height, depth, area, or volume)
- Identification: Labels are read and decoded for product identification and tracking (regardless of the type of 1D or 2D code used and its orientation)
System designers can choose between different image acquisition and lighting technologies to highlight the salient features of the object to be analyzed. The main distinction between the types of machine vision is that of 2D and 3D vision systems.
2D Machine Vision with Matrix or Linear Cameras
Depending on the application, two-dimensional images can be acquired through a matrix camera which instantly frames a two-dimensional field. A linear camera may also be used to acquire a single line of pixels and therefore needs a relative movement between the camera and the object to scan the second. The result can be a monochrome or color image, typically RGB. In both cases, the critical factor for good image quality is lighting. The three most used lighting techniques are:
- Direct lighting (for example, through a circular LED illuminator): The light is emitted from the front by a ring of LEDs placed around the optics. Ideal for obtaining excellent contrasts on opaque surfaces, this technique is not suitable for reflective surfaces
- Diffused lighting (for example, through a dome illuminator): The light that hits the object is indirect and therefore suitable for surfaces that would cause reflections with direct light
- Backlight: the object is positioned between the light source and the optics. Since it returns very precise information on the contours of the object, this technique is mainly used for measurement and positioning procedures.
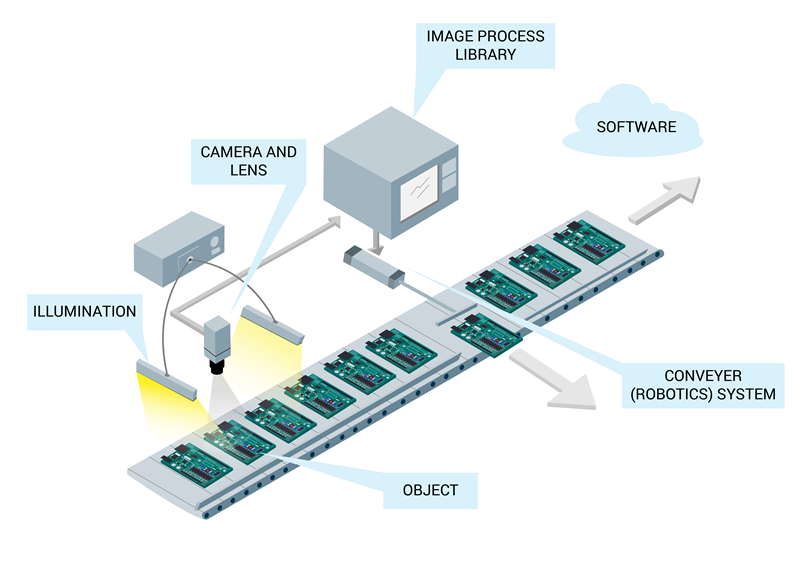
2D computer vision is particularly suitable for all applications where high contrast is required or when color or texture is relevant. For the application to be robust, the chosen lighting method must allow the acquisition of images with high contrast between the object to be analyzed and the background.
3D Machine Vision Reconstructs the Shape and Size of an Object
The acquisition of three-dimensional images can be carried out in different ways, which can be divided mainly into two categories: scanning and snapshot-based techniques
The scanning technique is typical of laser triangulation systems in which a laser blade draws the object's profile as it moves under the camera or if the vision system is moved over the stationary object. Subsequent profiles are acquired from the camera and then put together to create a 3D image of the object. Typically, an encoder signal is used to ensure that successive profiles are equidistant even in the event of speed variations. This technology allows the object to be reconstructed with high precision.
Snapshot-based technologies use different approaches to reconstruct the shape and position of objects in space. For example, Time-of-Flight (ToF) technology measures the time of a light signal emitted by a source placed close to the sensor. In this way, it is possible to calculate the distance of the obstacle encountered in a particular direction, thus reconstructing a three-dimensional point cloud that approximates the shape of the framed object. The accuracy of the reconstruction is lower than the scan-based technique.
3D artificial vision provides information relating to the height and distance of objects. As a result, it is preferable for the dimensioning of volumes, the analysis of the object's three-dimensional shape, and the identification of the position and orientation of objects that, if acquired in 2D, would result in low contrast. Identifying the orientation of the pieces in Bin Picking applications provides a relevant example.
In addition to choosing the best technology for image acquisition, the setup of a vision system can vary significantly based on the complexity of the analysis required. It can range from the simple installation of a configurable vision sensor, which may be done by an inexperienced user, to the creation of a complex project, which includes the more advanced development of software programs and algorithms. However, this flexibility – typical of artificial vision – makes these systems more efficient and robust in challenging applications compared to traditional sensors.
Whether using 2D or 3D imaging, the artificial intelligence deployed in machine vision provides a level of precision that is equal to, and in some cases, even better than human inspection. Accelerated speed-to-market is a considerable advantage as well. Based on these high-value benefits, machine vision is the way of the future for optimizing industrial automation systems.